The Crawford County Historical Society sponsored construction of this
replicate historic woodfired
“groundhog” pottery kiln starting in 2005 with most of the effort occurring
in 2006 and
early 2007. The first firing of pottery was on May 18, 2007 during the
Jugfest/Old Knoxville
Days festival centered at the 1852 Historic Crawford County Courthouse
in Knoxville Georgia.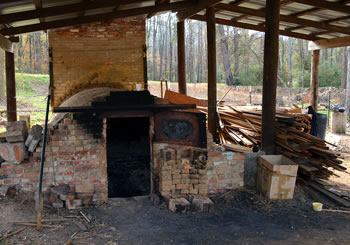
The Historical Society had three objectives in mind when they formed a
loose-knit partnership
with Shelby West to create the kiln.
First, the kiln demonstrates a critical part of life in the 1800s and
early 1900s in Crawford
County – the making of utilitarian pottery for everyday use and for sale.
Pottery was an
important part of the local economy with "jugmakers" supplying
stores, breweries and hospitals
throughout the state. Additionally, the kiln provides educational opportunities
to the local
community and visitors in art, crafts, geology, migration patterns, and
historic daily life styles.
Second, the kiln provides a method for promoting Crawford County's contributions
to the state's
growth and economy and to development of the pottery craft. As a focal
point for visitors, it
promotes heritage tourism. It will support exhibits, pottery classes
and other events in the
Cultural Center that eventually will be a part of the historic 1852 Crawford
County Courthouse
which is “just up the road” approximately 200 yards from the kiln.
Third, sale of pottery from the kiln financially benefits area potters,
thereby helping to revive the
pottery tradition, and Historical Society projects such as the Cultural
Center and Historic Courthouse.
While the Historical Society was the focal point for construction of
the kiln, many people from
the community and many supporters from around the state were also involved.
Local landowner
Bryant Pyles allowed use of his land for the project. He and several
members of his family, who
are descendants of early potters, contributed funds, materials and labor.
Local potter Shelby
West conceived, planned and provided a great part of the labor for this
project. Local potters
Charlie B. West and Mark Merritt were also involved as were collectors
from Texas, researchers
from Alabama, and many citizens and pottery enthusiasts from Crawford
County. Owners of the
former Merritt Pottery, a local bricklayer, and a pottery lover from
South Georgia donated
bricks. Two local businessmen purchased two loads of special fire brick
and brought them from
Athens, Georgia to Crawford County at their own expense. Another provided
the trailer and yet another loaned a brick saw. Both the Crawford County Commission and the
Roberta-Crawford
County Chamber of Commerce supported the construction and use of the
kiln. Area newspapers
and television stations have covered various events to help publicize
the project.
Shelby West was uniquely qualified to lead the kiln project. He first
became interested in
pottery in his high school art class where his pieces were fired in an
electric kiln. While
attending Barry College he assisted with art classes during the summer
and began to read more
about Crawford County potters, their history, and their techniques. This
led him to a
commitment to learn to create pottery using historic techniques and materials.
Using
photographs in a book he built a potter’s kick wheel from salvaged oak
wood. He learned where
to dig his clay and then ground it in his homemade mill. He then learned
to duplicate the historic
alkaline glazes which he uses for all his pieces. His first “groundhog”
kiln was a small one at his
parent’s Crawford County home so he could be certain his kiln design
and technique would work
satisfactorily. Then he constructed a large version (shown in the photograph)
at his home in Adairsville, Georgia. From there he has amassed a large body of work,
all produced with
historic techniques and materials.
Mark R. Merritt was another valuable participant in the kiln construction.
He is a 6th generation
Merritt/Crawford County potter. Mark considers himself a modern Crawford
County potter in
that he produces pieces of traditional style using modern glazes and
techniques. Mark and his
family also manufacture clay for use in pottery at Lizella Clay Company,
a business founded by
his father, Ray, more than forty years ago. Mark is descended from a
long line of Crawford
County potters. He is a grandson of the late Jewel Merritt, a great-great
grandson of the late
Jackson (Jack) Merritt, and a great-great-nephew of William (Billy) Merritt,
all well known
potters.
Shelby’s father, Charlie B. West, also made major contributions to the
construction and
operation of the kiln. He became interested in pottery “throwing” as
he and his wife, Marcia,
encouraged and supported Shelby as he was developing his historic and
traditional techniques
and processes. Since then, under Shelby’s tutelage, he has become a proficient
potter in his own
right. Charlie and Shelby together haul in the wood to feed the kiln
fire, load the pieces into the
“ware-bed,” along with volunteers tend the fire for approximately ten
to twelve hours, and
finally remove the cured pieces for final cooling and display. He teaches,
along with Shelby
and Mark Merritt, at the one-session pottery classes the Historic Society
offers to elementary and
high school art pupils and adults as part of the Jugfest elebration
so we can further our pottery
traditions. Charlie has in his personal pottery collection a signed and
dated piece from every
firing of the Knoxville Bottom kiln.
Initial construction of the kiln (including a fence and access gate)
represents a total cash
investment of $3300 ($2450 for bricks and bricklayer labor, $450 for
the shelter over the kiln,
and $400 for the fence and gate). These funds were provided by donations
from the community
($1900) and the Historical Society ($1400). In addition, there were direct
donations of materials
and, of course, the labor to construct the kiln. In 2009 the original
shelter over the kiln proper
was expanded at a cost of $500 for materials and with donated labor to
include the area in front
of the entrance. This makes it much easier to tend the fire during inclement
weather and
provides additional space to protect fire wood from the weather. In 2013
the Historical Society
allocated $1500 for materials for Shelby West to renovate the kiln’s
chimney. This type of kiln
requires continuous repairs and up-grades because of the damage resulting
from the intense heat
generated during a firing.
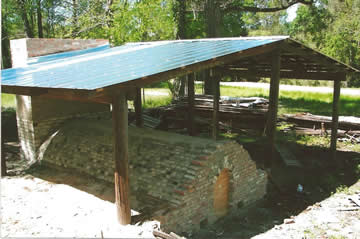
Since the kiln became operational in 2007 it has been fired about four
times a year, one of the
four as part of the Jugfest/Old Knoxville Days festival. For each firing
potters from throughout
the state and elsewhere are invited to bring their wares, and an average
of five potters usually
participate. They come from around Georgia and surrounding states. Pieces
are fired for local
high school students learning about pottery in their art class. Middle
school students visit the
kiln during firings on field trips. A young potter from Demorest in North
Georgia recently
became interested in pottery and the woodfired method and has taken part
in two firings. Other
potters participate in order to see the results of their efforts completed
in a historically accurate
process.
Each time the kiln is fired generally 10 to 20 visitors help stack wood,
feed the fire, provide hot
chocolate and coffee, and offer moral support. The ten-to-twelve hour
process gives the potters
opportunities to discuss methods and history and to educate visitors.
For the glazes being used a temperature of 2350 degrees to 2400 degrees
is maintained in the
kiln by adjusting the size of the fire and the amount of air flowing
across the pieces. Kiln
temperature is determined with a series of “temperature equivalent” pyrometric
cones each of
which deform or melt at a specified temperature. The number of pieces
in a particular firing,
their relative sizes and masses, and the potter’s experience with this
type of kiln govern the
arrangement of the pieces within the kiln so that the glaze is vitrified
(melted) and the pieces
don’t crack. Having the glaze vitrified means the container will not
leak when filled with liquids
and they can be used in an oven or microwave. The firing duration for
a particular kiln load
depends on, for example, the moisture content of the atmosphere or if
there are air leaks around
some bricks (from a previous firing) affecting how long it takes to achieve
the desired
temperature.
Most of the firings are followed (after a cooling period) by a round-robin
sale. Participating
potters price their goods. One at a time buyers select one piece in the
order in which they
register for the sale. When all buyers have made their selections, the
process is repeated until
there are no more pieces or no more buyers. The Historical Society collects
a buyer's premium
and manages the sale process.
Pottery collector and researcher Patricia Keller describes the kiln reproduced
by the Society as
being similar to “groundhog” kilns that are uniquely southern kiln types
which were used to fire
alkaline glazed pottery in the 19th century. The groundhog kiln was semi-subterranean
in
construction featuring a doorway leading into a long, low passage of
brick or rock construction
terminating in a chimney poking out of the ground up hill from the entrance.
The ware was
loaded in the low passageway or "ware-bed" and the fire was
built in the sunken firebox located
just inside the door. The chimney drew the heat from the fire through
the pottery inside. This
type of firing or " burning " worked well with large pieces
of pottery. Later, when potters made
more and more smaller items, they found that kilns shorter in length
but with higher ceilings
were better for insuring that each small piece was fired and glazed properly
(Zug 1986:401). The
Knoxville Bottom type of kiln is built entirely above the ground but
features some characteristics
of its ancestor, the “groundhog” kiln. It is still rectangular in both
plan and profile. The ware is
still loaded in a front door and there is a chimney in the rear. To replace
the insulation that
building into a hillside provided in the historic configuration, mounds
of dirt are built up on both
sides of the kiln. There also is a firebox located just inside the door.
This later configuration of a
wood-fired kiln also provides a cross-draft airflow with a fire at one
end creating hot air that
flows to a chimney at the other end. In this respect it is similar to
the early "groundhog" kilns of
the Piedmont. The domed shape of the roof is achieved by erecting a wooden
frame that looks
like an upturned boat in the interior to support the firebricks of the
roof until the full structure is
complete and self-supporting. Once the top brickwork is complete, the
wooden frame is
removed.
|